Для передачи веса тепловоза на путь, создания тяговых и тормозных усилий и направления движения тепловоза по рельсам предназначены колесные пары (рис. 3), состоящие из оси, двух колесных центров, двух бандажей, двух стопорных колец и большого зубчатого колеса.
Ось 3, откованная из осевой стали, подвергнутая нормализации и механически обработанная, имеет цилиндрическую форму с различными диаметрами по длине в зависимости от назначения ее частей. Крайние части а диаметром 170 мм являются шейками под роликовые буксовые подшипники. Под-ступичные части в диаметром 205 мм предназначены для напрессовки колесных центров. Ступенчатый переход от шеек а к подступичным частям «осуществляется с помощью предподступич-ных частей б диаметрами 174 и 188 мм.
Подступичная часть г диаметром 210 мм используется для напрессовки большого зубчатого колеса. Такой же диаметр имеют две шейки д под моторно-осевые подшипники. Между шейками д заключена средняя часть оси е диаметром 196 мм. Все переходы от одного диаметра к другому (галтели) плавные с радиусом закругления не менее 20 мм, что позволяет избежать концентрации напряжений и появления усталостных трещин. Цилиндрические поверхности оси (кроме средней части) накатаны роликами и отшлифованы.
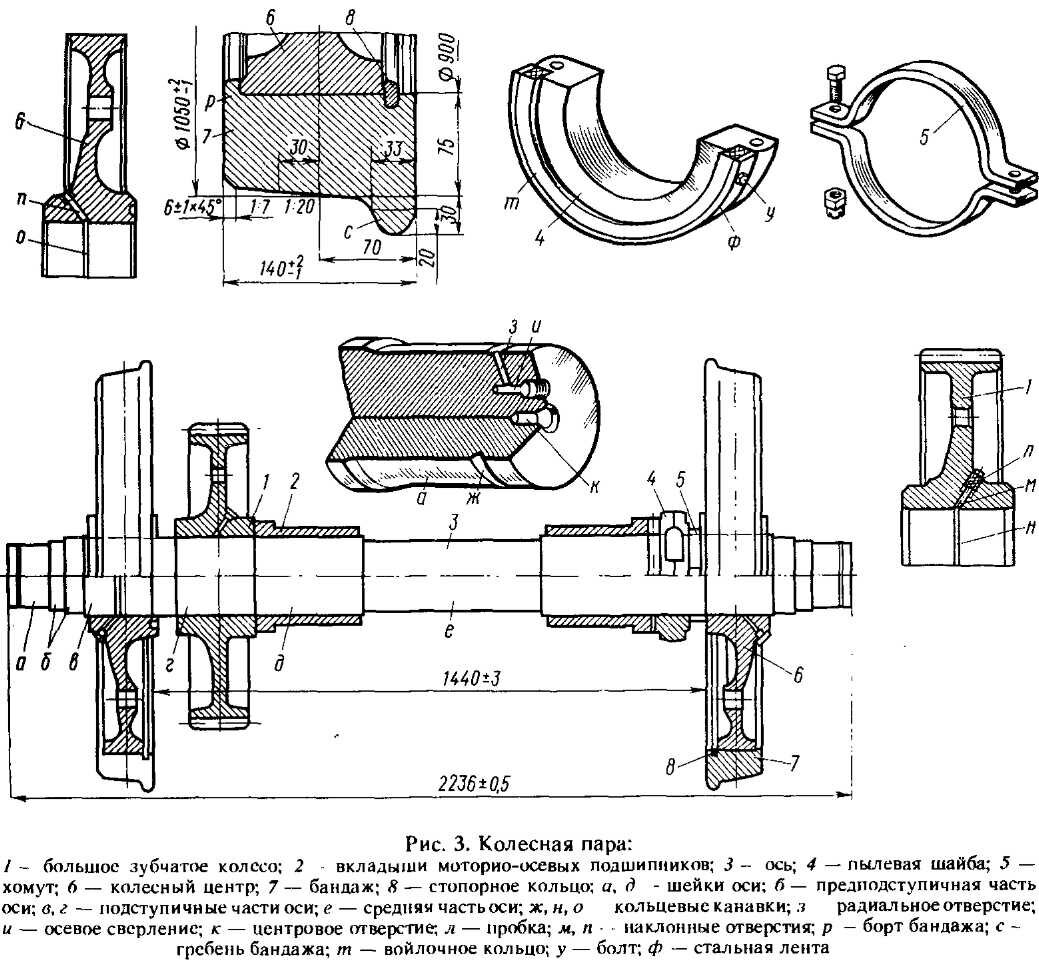
Конструкция оси предусматривает возможность демонтажа роликовых подшипников при полной ревизии букс. Для этого по торцам оси сделаны осевые сверления и диаметром 5 мм, соединенные радиальными отверстиями з диаметром 3 мм с кольцевыми канавками ж шириной 4 мм,проточенными на наружной поверхности буксовых шеек а. На конце осевого сверления и сделана расточка и нарезана резьба Ml6X1,5 под штуцер гидравлического пресса, которым нагнетают масло в канавку ж. При давлении 300 МПа (3000 кгс/см2) масло упруго деформирует шейку оси и внутреннее кольцо роликового буксового подшипника, просачивается между сопряженными поверхностями, что позволяет легко снять подшипник. По торцам оси в процессе механической обработки сверлят центровые отверстия ас диаметром 12 мм и глубиной 32,5 мм с последующей раззенковкой.
Большое зубчатое колесо 1 изготовлено из легированной стали и напрессовано на ось в холодном состоянии усилием 600 — 800 кН (60 — 80 тс). Для облегчения процесса напрес-совки отверстие диаметром 210 мм в ступице зубчатого колеса с двух сторон расточено под конус 1:20 на глубину 10 мм. Зубчатое колесо имеет 76 прямых зубьев, наружная поверхность которых закалена токами высокой частоты на глубину 2 — 5 мм с последующим низким отпуском (нагрев до температуры 170 — 180 °С и охлаждение на воздухе).
Для съема зубчатого колеса с помощью гидропресса в его ступице сделаны наклонное отверстие м диаметром 5 мм и кольцевая канавка н шириной 3 мм. В эксплуатации отверстие м закрыто пробкой л с резьбой М16х1,5.
Колесные центры 6 дискового типа отлиты из углеродистой стали и напрессованы на ось в холодном состоянии усилием до 1500 кН (150 тс) с натягом 0,3—0,4 мм. При этом колесные центры должны находиться на одинаковом расстоянии от середины оси. Отверстие в ступице колесного центра диаметром 205 мм с обеих сторон расточено под конус 1:10, что предотвращает задир сопрягаемых поверхностей. С этой же целью внутреннюю поверхность ступицы и наружную поверхность оси перед напрессовкой смазывают растительным маслом. Для спрессовки колесного центра с оси в его ступице также сделаны наклонное отверстие п и кольцевая канавка о.
Наружная часть колесного центра (обод) диаметром 900 мм соединена со ступицей диском, в котором имеются два отверстия диаметром 45 мм, используемые для транспортировки колесной пары и крепления ее при обточке на токарном станке.
Бандажи 7 изготавливают из раскисленной мартеновской стали, обладающей достаточной твердостью и одновременно вязкостью. Перед механической обработкой их подвергают закалке с последующим отпуском. Бандаж представляет собой сменное кольцо. На наружной поверхности бандажа, обработанной по специальному профилю, имеется гребень с, который направляет движение колеса по рельсу. Гребень плавно переходит в поверхность катания, состоящую из двух конических участков с уклоном 1:20 и 1:7 и торцовой фаски шириной 6 мм, выполненной под углом 45°. Участок поверхности катания с уклоном 1:20 обеспечивает устойчивое положение колесной пары на рельсах. Конический участок 1:7 позволяет колесной паре вписываться в кривые. При движении по кривой колесная пара под действием центробежной силы прижимается гребнем к наружному рельсу, т. е. наружное колесо катится по рельсу поверхностью, имеющей больший диаметр по сравнению с внутренним колесом. Следовательно, за один оборот колесной пары наружное колесо проходит больший путь, что позволяет избежать проскальзывания наружного колеса относительно рельса.
Торцовая фаска под углом 45° предусмотрена для того, чтобы выдавливаемый с поверхности катания металл заполнял ее, не вызывая уширения бандажа. Ширина бандажа 140 мм. Посередине его проходит круг катания — условная окружность для контроля состояния бандажа (замера проката, толщины и диаметра бандажа). Толщина нового бандажа 75 мм, а диаметр 1050 мм. На внутренней цилиндрической поверхности бандажа с одной стороны сделан борт р, ас другой проточена канавка под стопорное кольцо 8.
Перед насадкой бандажа на обод колесного центра его нагревают до температуры 250 — 320 °С, чтобы обеспечить натяг 1,0— 1,5 мм. В горизонтально расположенный бандаж опускают установленный на оси колесный центр до упора в борт бандажа. В канавку при температуре бандажа не ниже 200 °С заводят стопорное кольцо с? и на закаточном станке за-вальцовывают прижимной борт канавки вместе с кольцом.
При сборке на бандаже и колесном центре ставят контрольные риски. На бандаже выбивают керном 4 — 5 точек глубиной 1,0—1,5 мм на длине 25 мм и не ближе 10 мм к кромке упорного борта. На ободе колесного центра ставят затупленным зубилом риску глубиной до 1 мм. Для контроля за рисками в процессе эксплуатации на наружной грани бандажа, окрашенной белилами, наносят красную полосу шириной 25 мм, а на колесном центре как продолжение ее — белую полосу.
На ось собранной колесной пары надевают хомут 5 и пылевую шайбу 4. Обе детали разъемные и при сборке стягиваются двумя болтами. Пылевая шайба и хомут закрывают свободную часть оси и ограничивают разбег тягового электродвигателя (0,4 — 5,0 мм). Кроме того, пылевая шайба защищает моторно-осевой подшипник от загрязнения, для чего на цилиндрическом выступе шайбы ставят сменное войлочное кольцо т. Крепление кольца осуществляется стальной лентой ф, состоящей из двух частей, каждая из которых крепится тремя болтами у.
Подступичные части оси выполнены удлиненными, что позволяет производить сборку колесной пары как для колеи шириной 1520 мм (в этом случае расстояние между внутренними гранями бандажей 1440+3 мм), так и для колеи шириной 1435 мм.
Тележка | Маневровые тепловозы ЧМЭЗ, ЧМЭЗТ и ЧМЭЗЭ | Тяговый редуктор